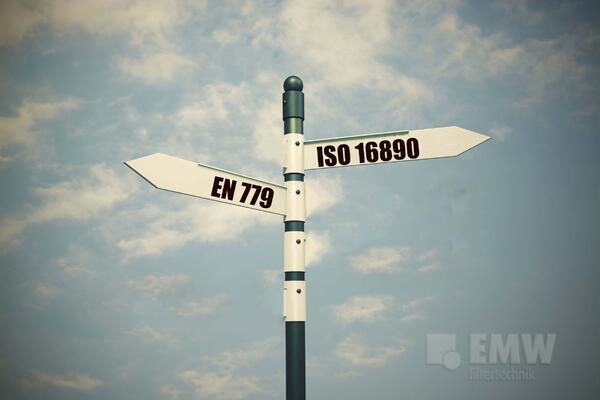
A common characteristic used to compare air filters is dust holding capacity, also known as test dust capacity. The text below will take a closer look at this term, its meaning, the test procedures used to determine it and its relevance to practice.
The dust retention capacity of an air filter is the mass of synthetic test dust retained by the filter until attainment of the specified final pressure drop increase.
Dust holding capacity was conceived as a test property serving as an indicator of an air filter's service life. If determined on two different filters according to the same test procedure, the filter with higher dust holding capacity should have a longer service life. So much for theory!
Direct comparison of dust holding capacity data is meaningful only if the test results evaluated were obtained using
Comparison of dust holding capacities determined with differences in any of these parameters is meaningless!
Test Standard | EN 779 | ISO 16890 |
---|---|---|
Test Dust | L1 (ASHRAE) test dust | L2 (ISO Fine) test dust |
Final pressure drop | 250 Pa for coarse dust filters | 200 Pa for ISO Coarse Filters |
450 Pa for medium and fine dust filters | 300 Pa for ISO ePM10, ePM2,5 und ePM1 |
Have you ever heard of ISO 15957? No? Well, here’s the low-down! This is a test standard which specifies the test dusts used to evaluate air cleaning equipment. ISO 15957:2015 defines 4 different dusts: L1, L2, L3 and L4.
The L1 dust specified in ISO 15957:2015, referred to as well as ASHRAE test dust, is familiar to industry experts from the well-known ASHRAE 52.2 test standard. DIN EN 779:2012, a well-known standard which was superseded by ISO 16890, also called for use of this test dust.
L2 dust has a variety of names. In ISO 12103-1 it is called A2 Fine Test Dust or sometimes "ISO Fine"– different names for the same dust! This dust is also specified in other standards including ISO 29461-1:2021 and ISO 16890:2016.
The EN 779 and ISO 16890 test procedures are found to differ not only in terms of the test dust used, but also in the pressure drop to which each is carried out. Our MPK 48-20 GT compact filter provides an example of this:
Filter Type | MPK 48-20 GT | MPK 48-20 GT |
---|---|---|
Test standard | EN 779 | ISO 16890 |
Dust Holding Capacity | 470g | 600g |
Test Dust | ASHRAE | ISO Fine |
Air flow rate | 3400m3/h | 3400m3/h |
Final pressure drop | 450 Pa | 300 Pa |
As shown by the table, dust holding capacities differ for the same product when tested according to EN 779 or ISO 16890. Again, dust holding capacity data may be compared only if determined under the same test conditions. If the tests used differ in any test parameter, you are in fact comparing apples and pears!
There is another point to keep in mind with regard to EPA and HEPA filter according EN 1822 and ISO 29463, dust holding capacity data commonly provided from some filter manufacturers. Neither the current version of EN 1822 nor the effective ISO 29463:2011 specify a defined dust intake procedure for EPA or HEPA filter classes! Even if a procedure of this type is specified, dust holding capacity testing of EPA and HEPA filters has only limited applicability to practice. This is because both types of filters are almost exclusively used in conjunction with a pre-filtration unit which reduces the particulate content of the ambient air before it enters these highly efficient filters.
To answer this question, EMW carried out field testing of air filters to permit correlation with their dust holding capacities in laboratory testing. In a project located in Central Europe, pocket filters from the ISO ePM10 55% (formerly M5) filter group were installed as pre-filters upstream of compact filters from the ISO ePM1 85% (formerly F8) filter group. Some of the compact filters were tested and weighed before installation. After two years of use over approx. 16,000 operating hours, the one half of the compact filters previously tested were retested and weighed again after one year of operation respectively 8,000 operating hours, the other half after two years of operation respectively 16,000 operating hours. The average weight gain due to this field use was around 255g per compact filter after one year of operation and around 486g after two years of operation.
At this point you may be thinking that a weight gain of 486g for a compact filter used for two years with an upstream pocket filter is nothing out of the ordinary. You’re right! The surprising thing about this was not so much the weight gain, but the increase in pressure drop across the filter. The pressure drop increased by only 23 Pa over this period.
The graph below compares performance data of the compact filter evaluated in laboratory testing and in field use. The red plot shows pressure drop as a function of dust holding capacity for the compact filters tested according to ISO 16890. The blue plot shows the same function determined in field use of the compact filters over a period of 1 year and 2 years, with approx. 8000 operating hours per year.
After one year of field use, the compact filters showed a weight gain of 255g and a pressure drop of only 138 Pa against 122 Pa in new condition. After two years of field use they showed a weight gain of 486g and a pressure drop of 145 Pa. However when the same compact filters retain 255g of L2 test dust (ISO-Fine) in laboratory testing, they show a pressure drop of 180 Pa and at 486g a pressure drop of 280 Pa (graph 1). Furthermore, the dust holding capacity required to cause a pressure drop of 138 Pa in the lab testing is only 95g and cause a pressure drop of 145 Pa only 127g (graph 2). As a result we can conclude that the laboratory test has nothing in common with real-world conditions.
In other words, the theory and practice of dust holding capacity are two totally different animals! Why are we going to the trouble here to explain all this to you? To make the point that it is extremely difficult or even impossible to draw conclusions concerning filter service life based on dust holding capacity. Also keep in mind that laboratory test dusts will usually differ substantially from the air particulates in the specific application at hand. Accordingly, various recently published standards – for instance ISO 16890 – contain the following disclaimer: „The performance results cannot by themselves be quantitatively applied to predict filtration performance in all ,,real-life” environments.” In addition, according to ISO 16890, the dust intake procedure is not mandatory for ISO ePM1, ePM2.5 and ePM10 filters, but may be performed optionally. We consider this to be correct. If you are looking for more reliable indicators for prediction of filter life, we suggest that you compare the ration of filter media area to initial pressure drop and efficiency.
Complicating matters further, test certificates issued according to ISO 16890:2016 may or may not be comparable to one another, i.e. may or may not refer to data determined under identical test conditions.
ISO 16890-2:2016 stipulates that the test method may be used for air flow rates between 900 m³/h and 5400 m³/h. When specifying the flow rate to be used by the test institution conducting the procedure, the filter manufacturer is free to choose the flow rate from this range. In the unlikely event the manufacturer does not specify a flow rate, the test is then carried out at 3400 m³/h.
The same applies to the test dust used. The ISO 16890-3:2016 standard stipulates that it can be used with any of the ISO 15957 test dusts, i.e. L1, L2, L3 and L4. However, an ISO 16890-3:2016 test report may only be issued for tests carried out with L2 dust (ISO Fine). Dust holding capacities obtained using any dust type other than L2 must be designated as such, i.e. as having been determined only in general accordance with ISO 16890-3:2016. Such data are generally described as resulting from testing "based on" ISO 16890-3:2016. Any wording of this type used to describe dust holding capacity data should immediately set off alarm bells in your mind. Classification of a filter as "ISO Coarse" is not permissible based on results obtained with any other test dust than L2 (ISO Fine).
The final pressure drop used in the ISO 16890-3:2016 procedure, i.e. the pressure drop to which the test is carried out, is also somewhat nebulous. ISO 16890-3:2016 specifies an final pressure drop of 200 Pa for ISO Coarse filters and 300 Pa for ISO ePM1, ePM2,5 and ePM10 filters, while requiring as well that any dust holding capacities given in test certificates be determined using this specified final pressure drop. However, an explanatory note in the standard also states that testing beyond these pressure drops is permissible as well.
Every so often, dust holding capacities can be found in other providers' promotional texts describing them as "Tested to 600 Pa final pressure drop" or "Tested to 800 Pa final pressure drop". As an expert in the area of dust holding capacity, you now know: Watch out!
A fine dust filter (F7-F9) was tested according to the EN 779 standard and has a dust holding capacity of 480g. To which final pressure difference is a fine filter tested according to EN 779?