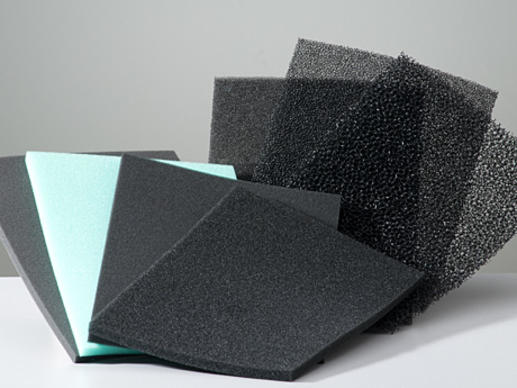
Specialists in reticulation of polyurethane foams, EMW® offers a broad portfolio of foam media including Poret® polyether as well as polyester foams in the pore densities PPI 10, PPI 20, PPI 25, PPI 30, PPI 45, PPI 60 and PPI 80. Our manufacturing facility includes reticulation reactors for roll stock as well as slabstock.
Slabstock dimensional capabilities:
Slabstock dimensional capabilities:
Roll-stock dimensional capabilities:
Reticulation is a post-foaming treatment which removes pore walls in closed-cell foam, creating an open pore network which permits fluid passage as required in filter media. The pore density, expressed in pores per inch (PPI), is a measure of closeness of neighbouring pores. The pores of a PPI 10 foam are far apart; those of a PPI 80 foam are more closely spaced.
Reticulation is carried out in a reactor. The closed-cell foam block or roll is placed in the reactor with a combustible mixture of hydrogen and oxygen which is then pressurized and ignited. The resultant explosion, carried out with controlled intensity, blows out the cell walls without impairing the strand structure or the properties of the filter foam matrix. The result is an open-cell foam with the desired pore structure.
The following magnified view shows closed-cell foam structure and the resultant open-celled foam structure created by reticulation.
Filter foams perform important tasks in highly diverse application sectors. Poret®, for instance, is utilized as a media for mechanical filtration, as a carrier for biological pollutant degradation and as an activated-carbon impregnated adsorption media. Its open-cell pore structure permits free circulation and flow of water, air and other fluids. Poret® is used in water filtration, wastewater treatment, exhaust gas treatment and air filtration,as well as in coalescers and oil filters.
The compression strength of a foam material is the amount of stress required to compress the material a predefined percentage, e.g. 40%, of its original thickness. A filter foam with low compressive modulus is softer and more pliable than one with high compressive strength.
Elongation at break is a measure of a material's deformation capability. It is determined in tensile testing, i.e. stretching a material sample under controlled conditions until it breaks. Elongation at break is the elongation, expressed as a percentage of the original sample length, at which breakage occurs.
Net density, expressed in kg/m³, is the weight of the foam product taking up a given volume. It is a key quality characteristic of filter foams. High-density foams are stronger and more stable than lower-density foams.
Tensile strength is another characteristic determined in tensile testing. The material sample is stretched until it breaks; the stress at which breakage occurs is the tensile strength of the material.